Since the birth of the car, people have not stopped the pursuit of car driving safety. The earliest seat belts and later airbags and other passive safety measures saved the lives of tens of millions of people, and later developed ABS (anti-lock brake system), ESP (electronic stability program), EBD (electronic braking force distribution system) ) And other active safety features have greatly improved the safety of the car again. But despite this, traffic accidents are still one of the biggest causes of unnatural deaths and injuries.
"With the increasing complexity of the system and the large number of applications of software and electromechanical equipment, the risk of traffic accidents due to system failure and random hardware failure is also increasing. Therefore, in recent years, a new car safety concept-safety prediction has emerged "During the" 2012 Industry and Technology Outlook Media Seminar "held recently, Dr. Yolanda, Global Product Marketing Manager, Freescale Asia Pacific Automotive and Industrial Solutions Division, pointed out that" safety predictions are some The system can detect failures in real time, and can pre-warn and prevent failures before they occur. This is the concept of automotive functional safety advocated by everyone. "To this end, Freescale has launched a safety assurance program named" SafeAssure ", which aims to Help system manufacturers more easily meet the requirements of functional safety standards in the automotive and industrial markets, and greatly reduce the difficulty of development and shorten the development cycle.
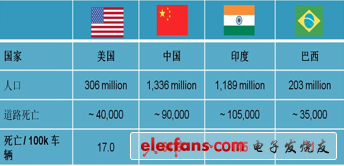
Figure 1: World Health Organization statistics: 1.3 million people die from traffic accidents worldwide each year, and 50 million people are injured.
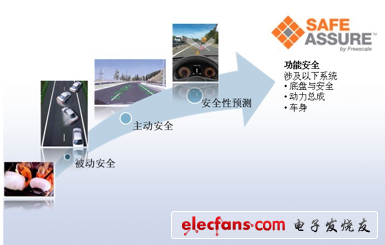
Figure 2: The evolution of automotive safety systems-the emergence of functional safety based on safety predictions.
From IEC61508 to ISO 26262, look at the evolution of automotive functional safety
Before the introduction of ISO 26262 in November 2011, the functional safety standard that the automotive industry complied with was the basic standard for functional safety of electronic, electrical and programmable devices, IEC 61508. However, as a general basic safety standard, for the particularity of the automotive industry, the standard has many shortcomings, especially under the conditions of increasing complexity of automotive systems in recent years. ISO 26262, derived from IEC 61508, is tailor-made for the current automotive industry. In particular, the requirements of ISO 26262 for hardware development and software development are suitable for the actual status of the current advanced automotive industry.
The ISO 26262 standard determines the safety requirement level from A to D (automotive safety integrity level-ASIL) for the system or a component of the system according to the degree of safety risk, where ASIL D level is the highest level and has the most stringent safety requirements. For system suppliers, these higher design requirements due to increased security levels must be met.
Security incidents are always accompanied by usual functions, quality-related R & D activities and product production. ISO26262 emphasizes all aspects related to the safety of R & D activities and product production, and provides a life cycle concept for automotive safety, providing necessary support during these life cycle stages. ISO26262 covers the overall development process of functional safety, including planning, design, implementation, integration, verification, validation and configuration.
SafeAssure
Two months before the launch of ISO26262, Freescale's SafeAssure safety assurance program was the first in the industry. "SafeAssure is a solution designed for functional safety standards in the automotive and industrial markets, helping companies simplify the process of achieving standards, shorten development time and reduce complexity." Yolanda pointed out, "Based on SafeAssure functional safety assurance solutions, manufacturers can easily achieve A to D and SIL-1 to 4 system safety standards. "
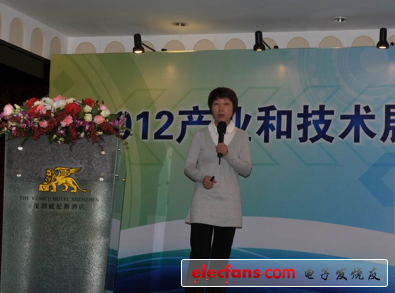
Figure 3: Freescale Xi Yunxia: Based on the SafeAssure functional safety assurance solution, manufacturers can easily implement system safety standards from ASIL-A to D levels.
The SafeAssure guarantee solution covers Freescale's technologies, including microcontrollers, analog and power management ICs, and sensors. The SafeAssure security assurance solution provides support to manufacturers in four aspects, including:
Safety process: Select those products whose definition and design aim to meet the requirements of various standards at the beginning, so that functional safety becomes an integral part of the product development process.
Safety hardware: Fault control is achieved through safety functions built into Freescale microcontrollers, power management ICs, and sensors, such as self-test, monitoring, and hardware-based redundancy. Freescale automotive analog device solutions provide additional system-level safety features, including checking microcontroller timing, voltage, and fault management.
Security software: comprehensive automotive functional security software products, including AUTOSAR OS, MCAL, driver and kernel self-test functions, and cooperate with leading third-party software providers to launch more security software solutions.
Security support: Freescale uses its extensive technical capabilities to provide customer training and system design audits related to functional safety architecture, as well as extensive security documentation and technical support.
SafeAssure's main goal is to simplify complexity. In order to simplify failure analysis, Freescale also provides an important analysis tool-failure mode, effect and diagnostic analysis (FMEDA). This tool analyzes the customer's entire data and the final result is not Meet the requirements required for functional safety. FMEDA tools can help customers calculate the final functional safety results according to their applications, so that the SafeAssure program can effectively simplify functional safety design work.
A motor with gearbox is a mechanical device utilized to increase the output torque or change the speed (RPM) of a motor. The motor's shaft is attached to one end of the gearbox and through the internal configuration of gears of a gearbox, provides a given output torque and speed determined by the gear ratio.
Motor with gearboxes are used in many applications including machine tools, industrial equipment, conveyors, and really any rotary motion power transmission application that requires changes to torque and speed requirements.
motor with gearbox,motor and gearbox,24v dc motor with gearbox,1hp motor with gearbox,12v electric motor with gearbox,small electric motors with gearbox
Shenzhen Maintex Intelligent Control Co., Ltd. , https://www.maintexmotor.com